Classification scheme for lean manufacturing tools pdf
The purpose of this paper is to present a classification of Lean models which aims to capture all the concepts related to this approach and thus facilitate its implementation.
The classification scheme is not intended as a decision-making tool. the proposed scheme does an excellent job of classifying all well-known lean manufacturing tools and metrics and suggests lean manufacturing tools and metrics that will help to address manufacturing problems. Lean manufacturing Lean manufacturing has been the buzzword in the area of manufacturing for the …
The aim of this paper is to examine the evolution of lean principles with the primary goal of converging towards a new set of principles that are more clearly aligned for the deployment of lean in engineer-to-order manufacturers. We take insight in lean production, lean project management, and lean product development in order to develop a set of principles which we suggest is more clearly
– First, we search for lean manufacturing books, books about Toyota Production System, lean thinking, six sigma and lean six sigma on Amazon.com, Goodreads.com, LinkedIn.com, News Sites and blogs related to lean manufacturing. The idea is to check how often books are mentioned to determine overall popularity.
journal papers and suggested different schemes of classification. In addition, certain gap areas are identified that would help researchers in further research.The paper has been categorized in four sections. Section one & two present introduction to Six Sigma and preamble to literature review respectively. Section three presents classification of Six Sigma papers based on research …
In contemporary manufacturing area, agility is considerably acknowledged as an emerging issue to react to dynamic market environment changes. The implementation of agile manufacturing system proved to be efficient to acquire a competitive advantage. Since the agile manufacturing (AM) concept was popularised in 1991, there is a growing
227 REFERENCES 1. Abbett, D. and Payne, V. “Gulfstream Value stream tour”, Presentation at Lean submit,1999. 2. Aberdeen group, “The manufacturing performance
The North East Productivity Alliance (NEPA) has disseminated selected lean manufacturing tools and techniques into companies in the North East of England. The aim of NEPA is to help companies improve productivity through applying lean manufacturing management practices and knowledge. The Industry Forum’s master class methodology is being used to transfer technology into local companies. This
The results were identical to those from the classification of the tools and metrics. nor conflicts between the existing definition of the tools and the definition of the tools as given by the classification scheme. to identify opportunities for waste elimination.Classification scheme for lean manufacturing tools Tool Cellular layout Facility layout diagrams Load leveling Six sigma Value
around the globe different lean manufacturing system become familiar and gain attraction towards scheme for lean tools. He proposed one scheme in which according to 7 criteria any lean tool …
An Empirical Study on Role of Lean Manufacturing in Manufacturing Industry Rajeev Choudhary *, The scheme of classification for lean manufacturing tools and …
Classification scheme for lean manufacturing tools S. J. PAVNASKAR, J. K. GERSHENSON and A. B. JAMBEKAR For the past few years almost every manufacturing industry has been trying to get ‘lean’.
The transfer of selected lean manufacturing techniques

Gershenson- Classification Scheme for Lean Manufacturing
presented a classification scheme for lean manufacturing tools. They have suggested that They have suggested that their classifications scheme enables companies to become lean and serve as a …
Similar to the Lean manufacturing principle of eliminating waste, the premise of the Lean application portfolio is to retire legacy or redundant applications in an organization’s application portfolio.
Lean layout is one of the lean manufacturing tools which have been applied in this automotive parts manufacturer. This tool encourages good visibility and management of the manufacturing system [2]. The U-shape design is incorporated in this case study in order to improve the efficiency of production. In this research, the current production layout is studied and the improvements are conducted
To help establish taxonomic guidelines and essential attributes for a manufacturing classification, investigations have been made into system classification and manufacturing classification. This provides a thorough understanding of the phenomena and will enable lessons to be learnt for application into a system theory based classification.
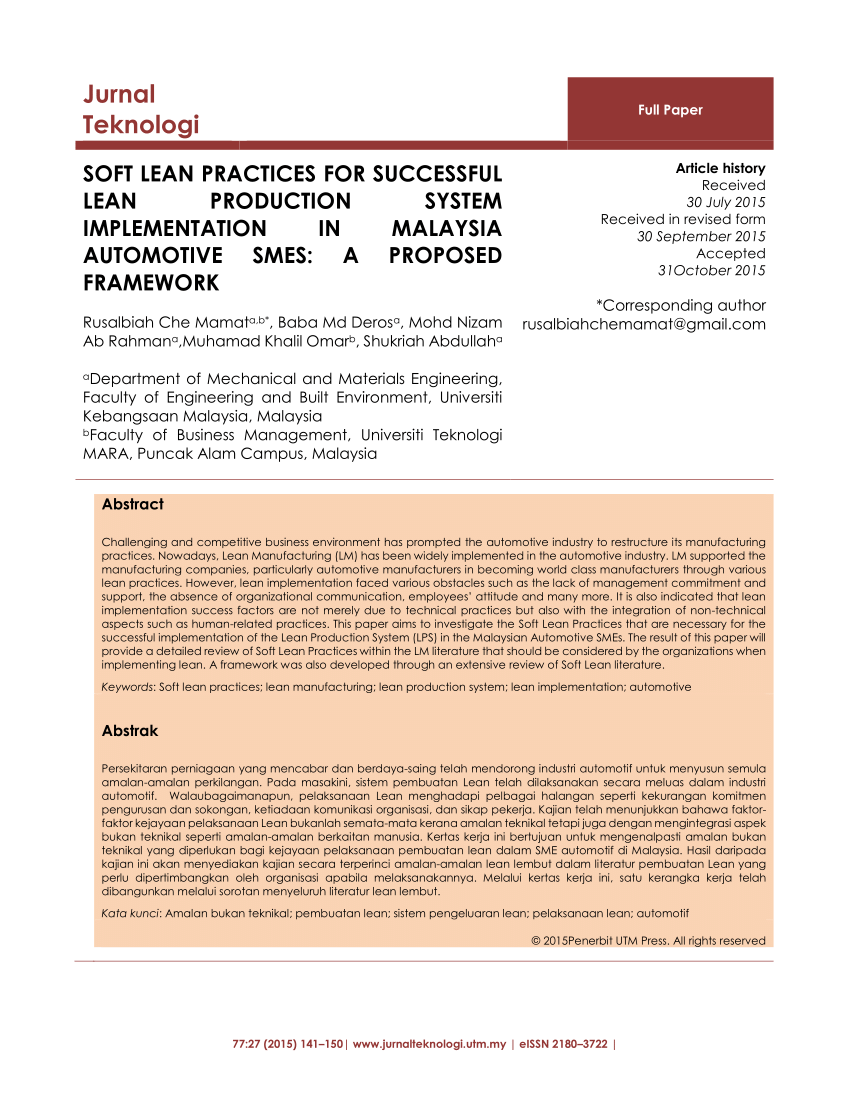
ABC classification is a ranking system for identifying and grouping items in terms of how useful they are for achieving business goals. ABC classification is closely associated with the 80/20 rule, a business metric that proposes 80% of the outcomes are determined by 20% of the inputs. The goal of
APQC’s Process Classification Framework (PCF) ® is the most used process framework in the world. It creates a common language for organizations to communicate and define work processes comprehensively and without redundancies.
Classification Scheme for Lean Manufacturing Tools Application of Lean Manufacturing Tools in a Garment Amorado, Application of Lean Manufacturing Tools in a Garment Industry
Insightful implementation of lean is necessary for high-value manufacturing and is complementary to strategic decision making regarding manufacture. However lean can be difficult to implement in specific organisations. One of the difficulties is deciding which of the many lean tools to apply and when to apply them. A complicating factor is

classification scheme to serve as a link between manufacturing waste and lean manufacturing tools. The proposed scheme classifies all well-known lean manufacturing tools and …
standard lean manufacturing. He goes on to suggest a series of features of agility and potential measures. He goes on to suggest a series of features of agility and potential measures. The main result of the audit was that of the five factors, customer sensitivity was the major concern.
This classification scheme systematically organizes lean manufacturing tools and metrics according to their level of abstraction, appropriate location of application of the tool in the
scheme to serve as a link between manufacturing waste and lean manufacturing tools. The proposed scheme classifies all well-known lean manufacturing tools and metrics. In addition, it suggests the tools and metrics that will help to meet manufacturing
flexible manufacturing system for engine and transmission parts machining. These decision These decision models are a first step toward developing practical business case tools that help industry to
1/08/2008 · Read “The transfer of selected lean manufacturing techniques from Japanese automotive manufacturing into general manufacturing (UK) through change agents, Robotics and Computer-Integrated Manufacturing” on DeepDyve, the largest online rental service for scholarly research with thousands of academic publications available at your fingertips.
Mckinsey Full Article – Download as PDF File (.pdf), Text File (.txt) or read online. Next frontier
In this paper we asses the current state of research on Lean Production and Supply Chain Management in the aeronautic industry, with two basic aims: 1) identify all lines of research developed, providing a classification criterion of literature, 2) discuss the empirical …
Measuring Response Capabilities in the Order Fulfillment
Aims to aid the construction of competent classifications that will advance the understanding of manufacturing system modelling and design. Supports proposals by novel comparisons drawn from the “science of diversity”, systematics, and the 200 years of experience that biological taxonomy has to …
“A Classification Scheme for Lean Manufacturing Tools.” International Journal of Production Research, Volume 41, Number 13, pp. 3075-3090. International Journal of Production Research, Volume 41, Number 13, pp. 3075-3090.
Part IV MANUFACTURING SYSTEMS Chapters: machines or with the aid of tools. Classification of production machines (worker participation): 1. Manually operated machines are controlled or supervised by a human worker. 2. Semi-automated machines perform a portion of the work cycle under some form of program control, and a worker tends the machine the rest of the cycle. 3. Fully automated
Gershenson- Classification Scheme for Lean Manufacturing Tools – Download as PDF File (.pdf), Text File (.txt) or read online. Classification Scheme for Lean Manufacturing Tools – pharmaceutical suspensions from formulation development to manufacturing pdf Pavnaskary et al. [17] have proposed a classification scheme to serve as a link between manufacturing waste and lean manufacturing tools. The proposed scheme classifies all well-known lean manufacturing tools and metrics. Also, it suggests the tools and metrics that will help to meet manufacturing problems. A customer-focused manufacturing strategy may be seen as comprising …
–Lean logistics, lean distribution, lean retail, lean accounting, lean office „ Cost issues, operational performance, environmental legislation and ageing assets are the biggest challenges for …
appropriate lean manufacturing tools. This classification scheme systematically organizes lean manufacturing tools and metrics according to their level of abstraction, appropriate location of application of the tool in the organization, whether it addresses management waste or activity waste, the type of resource waste it addresses, and whether it identifies waste, measures waste, eliminates
scheme for tools and techniques used. Some researchers [3] discussed tool sets in three Some researchers [3] discussed tool sets in three groups; statistical tools, process tools, and team tools.
Another scheme of classification for lean manufacturing tools and allied detailing proposed by Pavnaskar et al. (2003) are also quite exhaustive. Chitturi et al. (2007) explored practical issues in job shop using a standard VSM and also explained how improved VSM can eliminate some limitations of old VSM. Al-Sudairi (2007) built a simulation model to study the impact of certain lean principles
classification scheme to guide lean implementation in this sector. Features of a typical lean manufacturing model include one unit at a time production; non-value added time eliminated production in the work content time only, and relocation of required resources to the point of usage. In the present day of manufacturing, the assembly line can be formed easily for any industry whether it is a
This paper proposes a classification framework for performance metrics for smart manufacturing systems. The discussion focuses on agility, asset utilization, and sustainability, and we discuss classification themes for each of these areas that lead to the development of a generalized classification framework.
The main idea of lean manufacturing is actually simple and means relentlessly work on eliminating waste from the manufacturing process. However, after implementing these systems, many organizations find it difficult to achieve the desired results of them.
Findings – The paper proposes a classification scheme for the current research on ERP and lean production, which identifies six major areas in the extant literature. The literature survey is used to find existing research gaps and provides a research framework for future research directions regarding applications and implications of ERP systems in lean production. Originality/value – This
S. J. Pavnaskar et.al.; 2010 Classification scheme for lean manufacturing tools. Ma Ga Yang et.al. ; 2010 The impact of Lean Manufacturing and Environmental Management on business performances.
Download PDF . Recommend Documents have proposed a classification scheme to serve as a link between manufacturing waste and lean manufacturing tools. The proposed scheme classifies all well-known lean manufacturing tools and metrics. Also, it suggests the tools and metrics that will help to meet manufacturing problems. Detty and Yingling [12] quantified the benefits of conversion into lean
potential efficiency improvements is lean manufacturing or lean production, a set of tools to assist in the identification and elimination of waste. Lean classifies waste into seven categories: overproduction, transportation, rework/defects, over-processing, motion, inventory, and waiting. Utilizing economic data, one can track the inventory and transportation time along with the flow time (i
And, it was proven that lean manufacturing is the best manufacturing system in the 21 st century. The main objective of this paper is to investigate the extent of 24 lean manufacturing practices implementation in SME. Secondly, to determine the possible barriers that could influence the process of lean manufacturing implementation. A survey questionnaire was developed to collect top and senior
The Use and Impact of Manufacturing Productivity Improvementud Tools and Methodologies within the Automotive Component Industry
A Framework to Determine the Effectiveness of Maintenance
JEL CLASSIFICATION: D40, L11, L25, L81, M30, M40, M41. INTRODUCTION To become globally competitive modern manufacturing companies apply Toyota Production System (TPS). A pioneer in the application of the concept of lean is the Toyota Motor Corporation. It is designed as a set of tools and methods to eliminate waste and inefficiency in the production system and it is known as the Toyota
manufacturing tools and developed a seven-level classification scheme to categorize these tools. Monden (1993), Karlsson and Åhlström (1996), Detty and Yingling (2000), Sánchez and Pérez (2001), Motwani (2003), Bhasin and Burcher (2006) and Shah and Ward (2007) discuss some of the more commonly implemented lean manufacturing tools. Table 1 identifies these tools and classifies …
Analyzing and improving the productivity of labor-intensive manufacturing and assembly operations remains a crucial task for industrial companies.
a production management system that integrates Lean construction process with BIM. The VisiLean The VisiLean project follows the original research on interaction of Lean …
Introduction: This article shows the results of the applied research project “Improved design of the manufacturing process of wooden pallets through tools for increasing productivity.
existing lean manufacturing tools often due to inadequate understanding of the purpose of tools. While tool descriptions abound, there is no way systematically to link a manufacturing organization to its problems and to the possible tools to eliminate these problems. The main purpose of this paper is to propose a classi-fication scheme to serve as a link between manufacturing waste problems
system and value stream mapping (VSM) is used as a basic lean manufacturing tool and some cellular manufacturing philosophies to find out the improved level of performance and productivity particularly in the garments section of Bangladesh.
Pavnaskar et al. have presented a classification scheme for lean manufacturing tools. They have suggested that their classifications scheme enables companies to become lean and serve as a foundation for research into lean concepts. Many researchers have contributed to the definition of lean manufacturing. Shah and Ward
Lean thinking is a manufacturing ideal that was pioneered by the Japanese Toyota Company and. lean production was coined to describe the concept called the Toyota production system.
Every manufacturing industry has put in continuous efforts for its survival in the current volatile economy. In order to face the situation, industries are trying to implement new and efficient techniques in their manufacturing operations. Some of the established tools in this context are lean
Value stream mapping literature review and implications

Manufacturing classification Lessons from organizational
However, the proposed scheme does an excellent job of classifying all well-known lean manufacturing tools and metrics and suggests lean manufacturing tools and metrics that will help to address manufacturing problems. This classification scheme will assist companies trying to become lean and can serve as a foundation for research into the science of lean.
Numerous tools and techniques have been developed to eliminate or reduce waste and carry out Lean concepts in the manufacturing environment. However, in practice, manufacturers encounter difficulties to clearly identify the weaknesses of the existing processes in order to address them by
Read “Lean manufacturing: literature review and research issues, International Journal of Operations & Production Management” on DeepDyve, the largest online rental service for scholarly research with thousands of academic publications available at your fingertips.
lean co-creation: effective way to enhance productivity In this paper research is done how lean manufacturing & co-creation both can be applied to emphasize the efficiency, productivity with eliminating the seven types of wastages.
A Review on 5S Implementation in Industrial and Business Organizations Arash Ghodrati1, which comes from lean manufacturing process. The 5S practice simplifies the workplace and maintenance system’s procedures, decrease waste and non–value added activities. It also improves quality, efficiency and safety. It is the most effective tool of control, which at least reduce or totally avoid
Lean 7 Wastes Mass Manufacturing Customer Order Waste Time in Value Stream. “Lead Time” (Time to Cash) Product Delivery Lean Manufacturing Customer Order Waste Time in Value Stream.Waste Characterization Mass vs.
The main idea of lean manufacturing is actually simple and means relentlessly work on eliminating waste from the manufacturing process. However, after implementing these systems, many organizations find it difficult to achieve the desired results of them. Thus, the lean manufacturing remains an important area of research. For the importance of
manufacturing systems for processing the work parts as well as segregating the components based on geometrical and manufacturing attributes. In this paper modern manufacturing system is compared with conventional manufacturing by means of performance
Integral Analysis of Labor Productivity ScienceDirect

LEAN PHILOSOPHY IN AIRCRAFT MAINTENANCE
Classification Schemes The classification scheme can be decided locally represent a consensus The greater the quantity or complexity of items, the more helpful it is to follow a ready-made classification scheme, which represents a consensus as to a helpful order of classes Classification schemes may be either: special, i.e. limited to a specific domain of interest; or general, i.e. aiming to
The Process Classification Framework was originally envisioned as a taxonomy of business processes and a common language through which APQC …
MTU Life-cycle Engineering Laboratory
IMPLEMENTATION OF LEAN ASSEMBLY LINE A CASE STUDY UPT
A Review on 5S Implementation in Industrial and Business
introduction to manufacturing processes 3rd edition pdf – The Use and Impact of Manufacturing Productivity CORE
LEAN PRODUCTION Y GESTIÓN DE LA ScienceDirect.com
Classification scheme for lean manufacturing tools
ERP systems in lean production new insights from a review
15 replies on “Classification scheme for lean manufacturing tools pdf”
Leave a Commentpresented a classification scheme for lean manufacturing tools. They have suggested that They have suggested that their classifications scheme enables companies to become lean and serve as a …
The Benefits of a Lean Application Portfolio Informatica US
The transfer of selected lean manufacturing techniques
S. J. Pavnaskar et.al.; 2010 Classification scheme for lean manufacturing tools. Ma Ga Yang et.al. ; 2010 The impact of Lean Manufacturing and Environmental Management on business performances.
Lean philosophy implementation in a forging company PDF
The North East Productivity Alliance (NEPA) has disseminated selected lean manufacturing tools and techniques into companies in the North East of England. The aim of NEPA is to help companies improve productivity through applying lean manufacturing management practices and knowledge. The Industry Forum’s master class methodology is being used to transfer technology into local companies. This
A Classification Scheme for Smart Manufacturing Systems
Classification Scheme for Lean Manufacturing Tools Lean
The aim of this paper is to examine the evolution of lean principles with the primary goal of converging towards a new set of principles that are more clearly aligned for the deployment of lean in engineer-to-order manufacturers. We take insight in lean production, lean project management, and lean product development in order to develop a set of principles which we suggest is more clearly
The Use and Impact of Manufacturing Productivity CORE
Lean philosophy implementation in a forging company PDF
Gershenson- Classification Scheme for Lean Manufacturing
The Process Classification Framework was originally envisioned as a taxonomy of business processes and a common language through which APQC …
LEAN PHILOSOPHY IN AIRCRAFT MAINTENANCE
A New Set of Principles for Pursuing the Lean Ideal in
IMPLEMENTATION OF LEAN ASSEMBLY LINE A CASE STUDY UPT
Classification scheme for lean manufacturing tools S. J. PAVNASKAR, J. K. GERSHENSON and A. B. JAMBEKAR For the past few years almost every manufacturing industry has been trying to get ‘lean’.
MTU Life-cycle Engineering Laboratory
Integral Analysis of Labor Productivity ScienceDirect
ERP systems in lean production new insights from a review
Similar to the Lean manufacturing principle of eliminating waste, the premise of the Lean application portfolio is to retire legacy or redundant applications in an organization’s application portfolio.
Value stream mapping literature review and implications
Another scheme of classification for lean manufacturing tools and allied detailing proposed by Pavnaskar et al. (2003) are also quite exhaustive. Chitturi et al. (2007) explored practical issues in job shop using a standard VSM and also explained how improved VSM can eliminate some limitations of old VSM. Al-Sudairi (2007) built a simulation model to study the impact of certain lean principles
(PDF) LEAN MANUFACTURING IMPLEMENTATION DEVELOPING
Improving the manufacturing process of wooden pallets A
Classification Scheme for Lean Manufacturing Tools Lean
Introduction: This article shows the results of the applied research project “Improved design of the manufacturing process of wooden pallets through tools for increasing productivity.
Classification Scheme for Lean Manufacturing Tools Lean
An updated literature review of agile manufacturing
Mckinsey Full Article – Download as PDF File (.pdf), Text File (.txt) or read online. Next frontier
Measuring Response Capabilities in the Order Fulfillment
LEAN PHILOSOPHY IN AIRCRAFT MAINTENANCE
Classification scheme for lean manufacturing tools S. J. PAVNASKAR, J. K. GERSHENSON and A. B. JAMBEKAR For the past few years almost every manufacturing industry has been trying to get ‘lean’.
(PDF) LEAN MANUFACTURING IMPLEMENTATION DEVELOPING
Measuring Response Capabilities in the Order Fulfillment
Every manufacturing industry has put in continuous efforts for its survival in the current volatile economy. In order to face the situation, industries are trying to implement new and efficient techniques in their manufacturing operations. Some of the established tools in this context are lean
PROCESS CLASSIFICATION FRAMEWORK Arkonas.com
standard lean manufacturing. He goes on to suggest a series of features of agility and potential measures. He goes on to suggest a series of features of agility and potential measures. The main result of the audit was that of the five factors, customer sensitivity was the major concern.
lean manufacturing tools [PPT Powerpoint] – vdocuments.site
JEL CLASSIFICATION: D40, L11, L25, L81, M30, M40, M41. INTRODUCTION To become globally competitive modern manufacturing companies apply Toyota Production System (TPS). A pioneer in the application of the concept of lean is the Toyota Motor Corporation. It is designed as a set of tools and methods to eliminate waste and inefficiency in the production system and it is known as the Toyota
LEAN PRODUCTION Y GESTIÓN DE LA ScienceDirect.com
MTU Life-cycle Engineering Laboratory
Lean thinking is a manufacturing ideal that was pioneered by the Japanese Toyota Company and. lean production was coined to describe the concept called the Toyota production system.
MTU Life-cycle Engineering Laboratory
The Benefits of a Lean Application Portfolio Informatica US
Comments are closed.