Wind turbine blade manufacturing process pdf
5/04/2007 · Advanced materials for turbine blade manufacture. 05 April 2007 Philippe Christou. Advanced composite materials and technologies, particularly direct manufacturing processes such as resin infusion are becoming the preferred manufacturing choice across the wind turbine industry.
This will allow Siemens to dispatch all of the constituent parts that make up a wind turbine from one location, once blade production begins later this year. The blade manufacturing process will be housed in a large steel-framed multi-span braced structure measuring approximately 300m long × …
THERMAL TO MECHANICAL ENERGY CONVERSION: ENGINES AND REQUIREMENTS – Composite Materials In Wind Manufacturing, Wind turbine, Blades Contents 1. Introduction 2. Wind turbine rotor blades: construction, loads and requirements 3. Composites for wind turbine blades: Main constituents and manufacturing 3.1. Fibers 3.2. Matrix 4. Manufacturing technologies and defects 4.1. Manufacturing
A manual is designed to show the process of producing a wind turbine blade from fibre-glass This work is licensed under a Creative Commons Attribution …
There are two main methods for manufacturing wind turbine blades: prepreg and resin infusion. The The infusion process is commonly perceived as the most cost effective process …
Vacuum Infusion for Wind Blade Manufacturing Composites & Polycon 2006. Abstract • Vacuum infusion (VIP) is currently used by many blade manufacturers – 70% glass fiber/resin weight fractions • Aspects of the VIP process can bring certain fabrication challenges unique to blades, – Glass fabric placement – Fabric and fiber orientation control – Joint fabrication • Let’s examine
We expect the bio-based manufacturing process to be very similar in terms of blade performance, but to differ in terms of the cost over the life cycle of the blades. The present value of all recurring costs and residual value of the blade at the moment of being disposed are calculated in order to determine the best long term manufacturing process.
It is not clear which of these processes is most suitable for wind turbine blade production in this decade, but it is clear that the next generation of blades can meet their performance goals, and it is likely that one or more of these processes will achieve the cost objectives.
Wind Turbine Blades Using Thermoplastic Composite Material. Big Area Additive Manufacturing Used to 3D Print a Wind Turbine Mold Alex Roschli Research Associate Oak Ridge National Laboratory Manufacturing Demonstration Facility April 2017 SmartManufacturingSeries.com. Today, ORNL is a leading science and energy laboratory. SmartManufacturingSeries.com. The Manufacturing …
A wind turbine is a machine that converts the wind’s kinetic energy into rotary mechanical energy, which is then used to do work. In more advanced models, the rotational energy is converted into electricity, the most versatile form of energy, by using a generator.
— The design and manufacturing requirements for wind turbine blades subject to DNV certification. — A guideline for designers, manufacturers, operators, and regulators of wind turbines. — A technical and contractual reference document between clients, contractors, suppliers, consultants and
Wind Blade Manufacturing Innovation Sandia Energy

Wind Energy Gurit
According to ecodesign considerations and green manufacturing requirements, the choice of moulding process for the production of composite wind turbine blades must provide the existence of a
functioning of wind turbines. 2 Wind Turbine Control Systems The first wind turbine control systems were relatively simple. Used on stall-pitch, fixed-speed turbines, little more was required of them than starting the blades, stopping them and turning the nacelle into the wind. Turbines used today for commercial-scale wind farms are variable-speed, variable pitch and are considerably larger
Material deposition in the tool is only one of a string of labour intensive processes in the manufacture of a large wind turbine blades and a holistic automated blade manufacturing approach is perhaps required to see the true labour saving benefits.

The materials and structural characteristics of several kinds of wind turbine blades are introduced and analyzed as well as the advantages and disadvantages of blades composites in this paper. Then the manufacturing technologies between traditional and high-quality composite wind turbine blades are studied and compared in this paper.
A wind turbine is a machine for converting the mechanical energy in wind into electrical energy. If the If the mechanical energy is used directly by machinery, such as a …
This was the basic mould manufacture process used. 1: Firstly, a wooden wind turbine blade sample was built. The process to make this blade, along with its size and shape, is given in ‘How to build a wind turbine: the axial flux windmill plans’ guide. This blade must be very accurately made as, once a mould is created, any imperfections will be repeated in all subsequent blades. 2: The
Wind to fabricate small (in comparison to traditional wind energy systems) wind turbine blades using large-scale polymer additive manufacturing (AM). The results of this project showed promise for the
The NREL blade model includes every step of the manufacturing process–from kitting to hand overlays to painting and final check‐off–for the vacuum‐assisted resin transfer molding process …
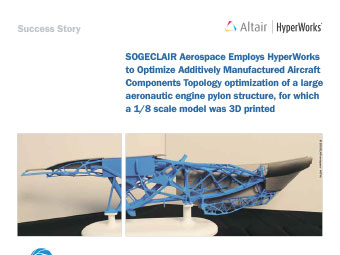
Operating a commercial wind turbine blade manufacturing plant requires staffing and overhead costs which are not directly related to the fabrication cost of an individual blade.
OFFSHORE STANDARD DET NORSKE VERITAS DNV-OS-J102 DESIGN AND MANUFACTURE OF WIND TURBINE BLADES, OFFSHORE AND ONSHORE WIND TURBINES OCTOBER 2006 Since issued in print (October 2006), this booklet has been amended, latest in April 2007.
Wind Turbine Blades Manufacturing Improvements and Issues TPI Composites, Inc. Structural Composites Division Derek Berry 24 February, 2004
Wind turbine blades continue to be the target of technological improvements by the use of better designs, materials, manufacturing, analysis and testing. As the size of turbines has grown over the past decade, designers have restrained the associated growth in blade weight to less than would have been possible through simple scaling-up of past approaches. These past improvements are briefly
Turbine Blades
are made by forming wax copies of the blades and then immersing the copies in a ceramic slurry bath.
After each copy is heated to harden the ceramic and melt the wax, molten metal is poured into the hollow left by the melted wax.
Manufacture of Large Wind Turbine Blades ACMC in partnership with Vestas Blades IoW. The market for wind turbine blades has grown at an average rate of 24% over the last 10 years.
A wind turbine blade design inspired by a tree seed called Triplaris Americana is presented. The blade was designed by means of an analysis of the seed’s curvature and airfoil along its wingspan; the result is as a non-conventional horizontal axis wind turbine composed of three blades.
Therefore, despite its complicated process and high cost of production, investment casting is suitable for manufacturing of the complex structure of turbine blades. 7 3) Single Crystal Production: 3.1) Purpose of making single crystal turbine blade: Investment casting, which was discuss in the previous section, was first only able to produce equiaxed turbine blades. After the molten metal is
Composite materials forwind turbine blades Department of Mechanical, Chemical and Materials Engineering University of Cagliari, Italy 1. Outline of presentation •Use of composites in wind turbine blades •Manufacturing processes •Mechanisms of damage and failure in composite materials •Strengthanalysisand damage tolerance approach Department of Mechanical, Chemical and Materials
Abstract. According to ecodesign considerations and green manufacturing requirements, the choice of moulding process for the production of composite wind turbine blades must provide the existence of a common area of intersection engendered by a simultaneous interaction between quality, health, and environment aspects (i.e. Q, H, and E for
Turbine Component Manufacturing MFG Wind
A turbine blade is the individual component which makes up the turbine section of a gas turbine or steam turbine. The blades are responsible for extracting energy from the high temperature, high pressure gas produced by the combustor.
The U.S. wind market has grown substantially over the years into an increasingly complex supply chain. There are more than 500 U.S. manufacturing facilities specializing in wind components such as blades, towers, and generators, as well as turbine assembly across the country.
Prepreg and Infusion: Processes for Modern Wind Turbine Blades Chris Shennan 5th September 2013 . 1 ©2013 Hexcel Agenda Introduction Wind blades: requirements and drivers Prepreg and infusion technologies: comparisons Laminate morphology Mechanical performance Prepreg and infusion matrices: M79 Co-infusion Conclusions . Introduction . 3 ©2013 Hexcel Company Profile Technology …
6 Project Approach Over the course of this project, alternative materials, manufacturing processes, and structural configurations were identified and evaluated for their potential benefit for large wind turbine blades.
current manufacturing methods targeted around small wind turbine blade manufacture. Results conclude that the development of a process to manufacture a complete wind turbine blade in a single process is achievable and feasible.
A set of three blades was tested at a small-scale wind farm, producing power outputs on the order of 20 W at low wind speeds, comparable to an existing commercial turbine. Keywords Wind blade manufacturing Thermoplastic composites Vacuum assisted thermoforming
a wind turbine blade from fibre-glass. This guide stemmed from work trying to This guide stemmed from work trying to produce a 1.8m blade for a 1kW version of Hugh’s design for use in the
1/07/1986 · The preferred manufacturing process is aimed at producing wind turbine rotor blades for a wind turbine of the type illustrated in copending U.S. patent applicaton Ser. No. 351,896 filed Feb. 24, 1982 entitled “Wind Turbine Rotor Control System” assigned to the assignee of the present application and incorporated herein by reference. The preferred process of manufacture involves forming the – introduction to manufacturing processes 3rd edition pdf wind turbine blades and ensuring their high energy capture efficiency in practical operation, an overview of the knowledge, practices and relevant lessons learnt in laboratory testing and condition monitoring of full scale wind turbine blades are
Large Wind Turbine Blades • Dedicated Offshore Wind Power Systems: Alternative blade manufacturing technology: – Thermoplastic composites – 2 skins, 1 spar and many ribs assembled through welding – Rubber forming and diaphragm forming of individual parts Pre-cut laminate sheet material Infra red heating panels Rubber die Metal die Rubber press Final thermoplastic composite …
Home » Research & Development » Wind Manufacturing & Supply Chain » Advanced Blade Manufacturing While the blades of a turbine may be one of the most recognizable features of any wind installation, they also represent one of the largest physical challenges in the manufacturing process.
A key technology unique to the wind industry All blades for Siemens wind turbine platforms with power ratings from 1.3 to 6.0 MW and rotor diameters from 62 to 154 meters are manufactured using the patented IntegralBlade technology. The blades are made from fiberglass- reinforced epoxy resin, and their external design represents state-of-the-art wind turbine aerodynamics. The IntegralBlade
PONTIS ENGINEERING: INTRODUCTION CHALLENGES IN THE DESIGN AND MANUFACTURING OF LARGE WIND TURBINE BLADES NOVEMBER 2016 » Founded in 2007 » 25 Specialists in Composite Engineering Six Sigma trained
Turbine Component Manufacturing ValueCreation for Turbine Manufacturers – Lower warranty costs and higher customer satisfaction Well-crafted, high quality composite blades, nacelles and spinners that stand up to the rigors of nature and time are critical to turbine productivity.
Wind Blade Manufacturing Innovation Juan Camilo Serrano Fiber Glass Science and Technology Sandia National Laboratories · 2012 Wind Turbine Blade Workshop · May 30-31 2012
The objective is to provide basic information and understanding about the materials and manufacturing techniques for wind turbine blades. This document will cover the process methodology, advantages and disadvantages of different manufacturing techniques.
Download PDF Info Publication number US20110221093A1 The process of forming a wind turbine blade or other structure as disclosed herein can begin with engineering the shape of the desired blade and ascertaining the resulting stresses and loads to which various part of the blade will be subjected. Thereafter, construction of a corresponding mold, for example a two-piece mold with a top
This paper in particular deals with the integrated modeling of a pultruded NACA0018 blade profile being a part of EU funded DeepWind project. The manufacturing aspects of the pultrusion process
Prepreg and Infusion Processes for Modern Wind Turbine Blades
manufacturing process changes. • Blade designs that manufacturing processes can achieve • Perform extended testing of new blade designs: static, fatigue and field • Trial fit before bonding • Blades can be bladder molded and/or infused in one piece eliminating the bonding process • Fabrics can be pre-impregnated at the factory site • Blades can be built out of smaller
Composite manufacturing development for wind turbine blades. Dr Faye Smith April CEng, FIMMM, April 2010 . Contents 2 Background Policy What might 15% renewables look like? Realising the UK’s offshore potential Innovation for industrial evolution Focus on blade technology and composites Production method trends UK Composites Strategy Examples of research projects: i-Composites …
1/05/2012 · A method of manufacturing a wind turbine rotor blade is provided. Anticipated primary load paths within the rotor blade are predicted. Fibers of reinforcing material are dispensed onto a mold, having an orientation pattern of the fibers which is selected in dependence on the predicting step.
WIND ENGINEERING VOLUME 36, NO. 4, 2012 PP 365-388 365 Wind Turbine Blade Design Review P.J. Schubel* and R.J. Crossley University of Nottingham,Faculty of Engineering,Division of Materials,Mechanics and Structures,
It is the object of the invention to provide a wind turbine blade having properties of laminated products, i.e. high strength in comparison with the amount of material and lower production cotsts compared to solid products, but where the strength compared to the costs of manufacturing the blade is highly increased compared to prior art blades.
The main objective of this project is to create an energy pathway for the sustainability of wind energy. Specifically, we want: 6 SUSTAINABILITY OF THE WIND TURBINE BLADE MANUFACTURING PROCESS: A BIO-BASED ALTERNATIVE
iii ABSTRACT This report addresses trade and industry conditions for wind turbine manufacturing for the period 2003 to 2008. • Annual U.S. wind turbine installations increased from 1,672 to 8,545 megawatts (MW) from 2003 to
Wind Turbine Blade Michael Vinodh Raj1#, Andrews2, M. Deneshkumar3, Manufacturing and Thermal Analysis of Wind Turbine Blade 225 3. Joining the Two Sides of the Blade In the same way as followed above the other side of the blade is manufactured. Now the sections are filed to ensure a good contact between them. The edges of the blades are freed of burrs. The adhesive used in the process …
1 Project and manufacturing of turbine blades – Small wind power applications Mário João de Sousa Brito Abstract This thesis main objective was selecting a manufacturing process, as well developing a mechanical design, for a
manufacturing process. Basic material costs used in the model are obtained from a variety of sources. Materials and prices are based on the majority sales within the wind turbine blade manufacturing industry for that particular type of product and are assumed to be ‘volume’ prices where available. Wastage is set for each material individually. Analysing the VI and LRTM cost centres with
Testing and Condition Monitoring of Composite Wind Turbine

Structural design and manufacturing process of a low scale
As the location of wind turbine installations diversify to areas with varying wind classes, emphasis in the wind blade production process has shifted towards demonstrating the flexibility to supply a broader range of wind blade models designed for varying wind conditions. The trend towards multiple wind blade models requires advanced composite and production expertise, sophisticated process
careful selection process, the current manufacturing setup of Vestas is established as one that is lean and scalable, but nonetheless with the Vestas quality stamp on every single wind turbine sold.
Gurit serves wind turbine blade manufacturers with a complete offering—from Tooling (i.e. the design, production and supply of wind turbine blade moulds and related equipment), the development, production and supply of advanced Composite Materials to Technical Support and solutions for the repair of installed wind blades.
Wind Energy Industry Manufacturing Supplier Handbook is a publication of AWEA – BlueGreen Allliance – GLWN 7OV[V (JRUV^SLKNLTLU[! -YVU[ *V]LY 9V[LR 0UJ 6OPV )HJR *V]LY .HTLZH 7LUUZ`S]HUPH 4 MANUFACTURING SUPPLIER HANDBOOK FOR The Wind Energy Industry
Turbine manufacturing process SlideShare
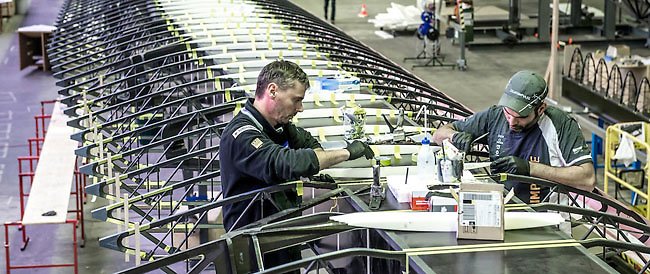
Study on Material Selection and Manufacturing Process of
DNV-OS-J102 Design and Manufacture of Wind Turbine Blades
CHALLENGES IN THE DESIGN AND MANUFACTURING OF LARGE WIND
SEP Collaborative Achieving a Sustainable Energy Pathway
– Vacuum Infusion for Wind Blade Manufacturing
Manufacturing and sourcing Vestas
Composite materials forwind turbine blades people.unica.it
(PDF) Ecomoulding of Composite Wind Turbine Blades Using
20 replies on “Wind turbine blade manufacturing process pdf”
Leave a Commenta wind turbine blade from fibre-glass. This guide stemmed from work trying to This guide stemmed from work trying to produce a 1.8m blade for a 1kW version of Hugh’s design for use in the
Project and manufacturing of turbine blades Small wind
Thermoplastic Composite Wind Turbine Blades ECN
UNITED STATES INTERNATIONAL TRADE COMMISSION
The U.S. wind market has grown substantially over the years into an increasingly complex supply chain. There are more than 500 U.S. manufacturing facilities specializing in wind components such as blades, towers, and generators, as well as turbine assembly across the country.
DNV-OS-J102 Design and Manufacture of Wind Turbine Blades
Method of manufacturing a wind turbine rotor blade
6 Project Approach Over the course of this project, alternative materials, manufacturing processes, and structural configurations were identified and evaluated for their potential benefit for large wind turbine blades.
Ecomoulding of Composite Wind Turbine Blades Hindawi
Cost modelling in polymer composite applications Case
US20110221093A1 Method and system for manufacturing wind
The objective is to provide basic information and understanding about the materials and manufacturing techniques for wind turbine blades. This document will cover the process methodology, advantages and disadvantages of different manufacturing techniques.
Turbine Component Manufacturing MFG Wind
WIND ENGINEERING VOLUME 36, NO. 4, 2012 PP 365-388 365 Wind Turbine Blade Design Review P.J. Schubel* and R.J. Crossley University of Nottingham,Faculty of Engineering,Division of Materials,Mechanics and Structures,
Advanced materials for turbine blade manufacture
We expect the bio-based manufacturing process to be very similar in terms of blade performance, but to differ in terms of the cost over the life cycle of the blades. The present value of all recurring costs and residual value of the blade at the moment of being disposed are calculated in order to determine the best long term manufacturing process.
Study on Material Selection and Manufacturing Process of
Wind Energy Industry Manufacturing Supplier Handbook is a publication of AWEA – BlueGreen Allliance – GLWN 7OV[V (JRUV^SLKNLTLU[! -YVU[ *V]LY 9V[LR 0UJ 6OPV )HJR *V]LY .HTLZH 7LUUZ`S]HUPH 4 MANUFACTURING SUPPLIER HANDBOOK FOR The Wind Energy Industry
Pultrusion of a vertical axis wind turbine blade part-II
Wooden wind turbine blade manufacturing process North
functioning of wind turbines. 2 Wind Turbine Control Systems The first wind turbine control systems were relatively simple. Used on stall-pitch, fixed-speed turbines, little more was required of them than starting the blades, stopping them and turning the nacelle into the wind. Turbines used today for commercial-scale wind farms are variable-speed, variable pitch and are considerably larger
Wind Manufacturing and Supply Chain Department of Energy
A turbine blade is the individual component which makes up the turbine section of a gas turbine or steam turbine. The blades are responsible for extracting energy from the high temperature, high pressure gas produced by the combustor.
Siemens wind turbine blade manufacturing facility Hull
1 Project and manufacturing of turbine blades – Small wind power applications Mário João de Sousa Brito Abstract This thesis main objective was selecting a manufacturing process, as well developing a mechanical design, for a
Study on Material Selection and Manufacturing Process of
5 MANUFACTURING PROCESSES FOR ROTOR BLADES
The objective is to provide basic information and understanding about the materials and manufacturing techniques for wind turbine blades. This document will cover the process methodology, advantages and disadvantages of different manufacturing techniques.
Method of manufacturing a wind turbine rotor blade
How wind turbine is made material manufacture used
5/04/2007 · Advanced materials for turbine blade manufacture. 05 April 2007 Philippe Christou. Advanced composite materials and technologies, particularly direct manufacturing processes such as resin infusion are becoming the preferred manufacturing choice across the wind turbine industry.
Wind Turbine Control Systems Mita-Teknik
Report on Manufacturing Wind Blades for Turbine Reliability
Cost Study for Large Wind Turbine Blades WindPACT Blade
Wind turbine blades continue to be the target of technological improvements by the use of better designs, materials, manufacturing, analysis and testing. As the size of turbines has grown over the past decade, designers have restrained the associated growth in blade weight to less than would have been possible through simple scaling-up of past approaches. These past improvements are briefly
Study on Material Selection and Manufacturing Process of
— The design and manufacturing requirements for wind turbine blades subject to DNV certification. — A guideline for designers, manufacturers, operators, and regulators of wind turbines. — A technical and contractual reference document between clients, contractors, suppliers, consultants and
Materials and Manufacturing Techniques for Wind Turbine
Manufacturing and sourcing Vestas
Blade System Design Studies Volume I Composite
5/04/2007 · Advanced materials for turbine blade manufacture. 05 April 2007 Philippe Christou. Advanced composite materials and technologies, particularly direct manufacturing processes such as resin infusion are becoming the preferred manufacturing choice across the wind turbine industry.
Wooden wind turbine blade manufacturing process North
Method of manufacturing a wind turbine rotor blade
A wind turbine blade design inspired by a tree seed called Triplaris Americana is presented. The blade was designed by means of an analysis of the seed’s curvature and airfoil along its wingspan; the result is as a non-conventional horizontal axis wind turbine composed of three blades.
Cost Study for Large Wind Turbine Blades WindPACT Blade
CHALLENGES IN THE DESIGN AND MANUFACTURING OF LARGE WIND
Wind Energy Gurit
According to ecodesign considerations and green manufacturing requirements, the choice of moulding process for the production of composite wind turbine blades must provide the existence of a
Large-Scale Additive Manufacturing for Low Cost Small
This was the basic mould manufacture process used. 1: Firstly, a wooden wind turbine blade sample was built. The process to make this blade, along with its size and shape, is given in ‘How to build a wind turbine: the axial flux windmill plans’ guide. This blade must be very accurately made as, once a mould is created, any imperfections will be repeated in all subsequent blades. 2: The
SEP Collaborative Achieving a Sustainable Energy Pathway
Turbine manufacturing process SlideShare
It is the object of the invention to provide a wind turbine blade having properties of laminated products, i.e. high strength in comparison with the amount of material and lower production cotsts compared to solid products, but where the strength compared to the costs of manufacturing the blade is highly increased compared to prior art blades.
CHALLENGES IN THE DESIGN AND MANUFACTURING OF LARGE WIND
Blade System Design Studies Volume I Composite
Vacuum Infusion for Wind Blade Manufacturing Composites & Polycon 2006. Abstract • Vacuum infusion (VIP) is currently used by many blade manufacturers – 70% glass fiber/resin weight fractions • Aspects of the VIP process can bring certain fabrication challenges unique to blades, – Glass fabric placement – Fabric and fiber orientation control – Joint fabrication • Let’s examine
Blade System Design Studies Volume I Composite
Comments are closed.