Root cause analysis examples in manufacturing pdf
The 5 Whys problem solving tool helps you with root cause analysis. The 5 Whys Example in Lean Manufacturing. The 5 Whys Example in Lean Manufacturing. The 5 Whys Example in the Lean Office . The 5 Whys Example in the Lean Office. Think about what you might do if you were to ask just one ‘Why?’ and then… As simple as the 5 Whys sounds, you will have to watch out for a few pitfalls
Free football border template introduction to philosophy pdf download event photography proposal pdf grade 2 english worksheets scientific method in real life situations lgbt subculture essay era of good feelings synthesis frontier airlines review imagery in common sense by thomas paine marie curie experiment radioactivity ap lang synthesis
RCA Name Manufacturing NCR Example. Report Number 522012 Report Date 5/2/2012 RCA Owner John Smith Root Cause Analysis Report Problem Statement
Root Cause Analysis: Designing for Root Cause Analysis As you have seen in this article, identifying root causes can be challenging. The best way to ensure you can identify root causes reliably is to design your business processes to make it easier.
ROOT CAUSE ANALYSIS OF DEFECTIVES OF A MANUFACTURING INDUSTRY. for the root cause of the pro blem. Figure 1 shows a . sample cause and effect diagram. Fig. 1 Sample cause …
“5W=1H” root cause analysis used in lean manufacturing. This training material is intended for experienced CT designers, manufactures and user as well as for managers with little or no knowledge of the Fish bone diagram.
Establishing a good root cause requires discipline and focus, but with practice, you will find the root cause quickly. The teams, who sit in a conference room and try to hash out a …
Root Cause Analysis in the food industry is a process or procedure that helps guide people to discover and understand the initiating causes of a problem. The goal of this process is to determine the missing or inadequately applied controls that will prevent a reoccurrence. With this mind, root cause analysis seeks to uncover and find the real cause of the problem and adequately deal with it
A Re-Examination of Failure Analysis and Root Cause Determination M. Zamanzadeh, E. Larkin and D. Gibbon Matco Associates PO Box 15580 Pittsburgh, Pennsylvania 15244 412-788-1263 December 2004 Failure analysis is a complex process applied to all different types of materials. Each class of materials requires special skills and experience to effectively unravel the causes of failure. This is the
Root Cause Analysis Definition. Root cause analysis (hereafter known as RCA) is a project management methodology used to identify the source of any issues or problems experienced in any process or product.
The following root cause analysis example incidents demonstrate how Cause Mapping can be used to document problems and identify solutions in various industries. Select an industry on the left to view its case studies on the right. Each example has a downloadable PDF to accompany the write-up.
And the most common method of analysis for these problems is the root cause analysis tools (root cause analysis training). You can also see Gap Analysis Templates . Analysing into a defect by inspecting into every single aspect of the problem in a step by step analysis is the root cause analysis example.
4 Root Cause Analysis for Drugmakers Introduction Wheneverregulatoryauthoritiesanywhereintheworldperformanauditofadrugmanufactur-er
The most common root-cause analysis technique in lean is the “Five Why’s.” This is practice of asking why repeatedly whenever a problem is encountered in order to get beyond the obvious symptoms to discover the root cause.
Root Cause Analysis for Drugmakers FDAnews
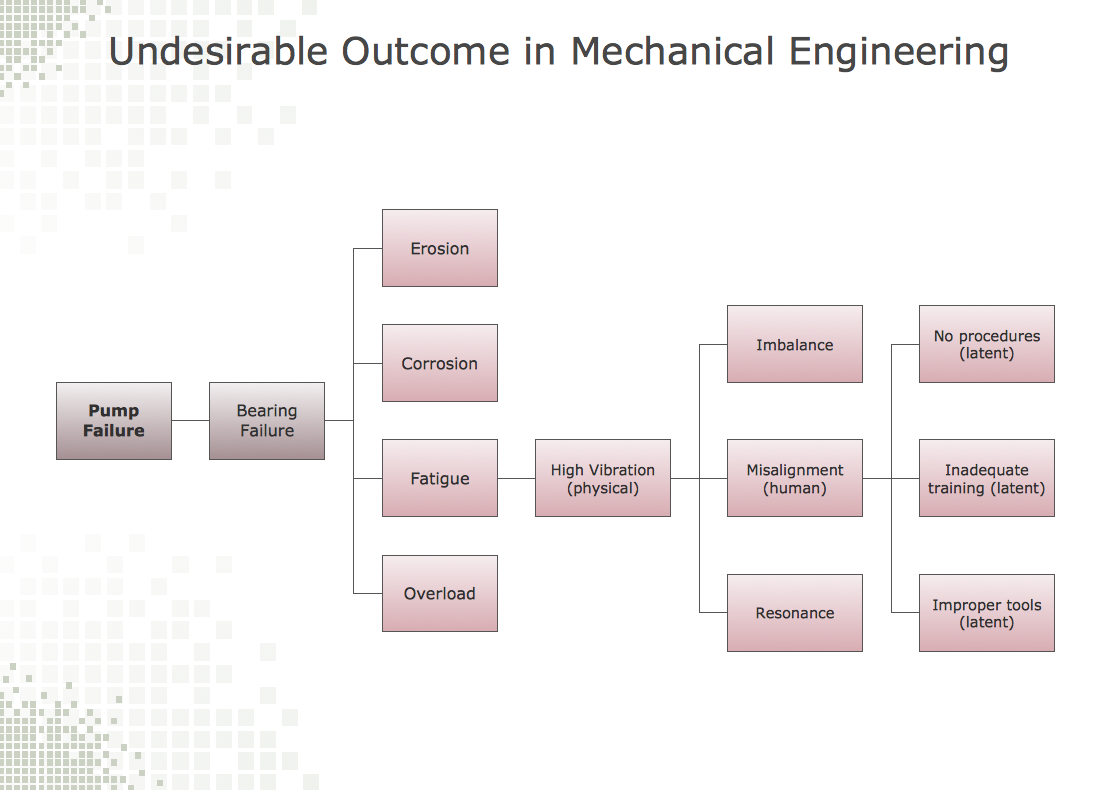
Root Cause Template Lean Enterprise Institute
Solving Manufacturing Problems 1. 8D Problem Solving Methodology 2. Containment 3. Defect Characterization 4. Failure Analysis 5. Defect Characterization Case Study 6. Root Cause Analysis Methodology 7. Prioritizing Corrective Actions 8. Validate that Corrective Actions Prevent Problem Recurrence 9. Leverage Countermeasures to Similar Products and/or Processes 10. Root Cause Analysis …
Failure Mode and Effects Analysis (FMEA) is a method designed to: Analysis is at the manufacturing/assembly process level. The Focus is on manufacturing related deficiencies, with emphasis on Improving the manufacturing process ensuring the product is built to design requirements in a safe manner, with minimal downtime, scrap and rework. manufacturing and assembly …
• Manufacturing • Management • Change Control • Purchasing/Supplier Quality • Testing • Documentation • Maintenance Many manufacturers tend to overuse training as a corrective action and do not adequately address the systemic corrective action. Root cause analysis tools • Commonly used tools – Fishbone diagrams – 5 “whys” – Fault-tree analysis – Among others. CAPA
Any time something unexpected happens, we could do some root cause analysis.” It’s important to note that the purpose of the 5 whys isn’t to place blame , but rather to uncover the root cause of why something unexpected occurred.
In lean manufacturing, root cause countermeasure tools are often used to help perform the necessary discovery and analysis, and to provide the insight needed …
Fault Tree Analysis, FTA FTA is performed in order to:! – analyze and show the connection between non-wanted events in the system and the root causes to these events!

The following RCA examples are based on genuine cases solved using the Apollo methodology and have been de-sensitized to maintain company privacy.
Root cause analysis moves maintenance from reactive to proactive in a systematic way. Getting to the real problem and underlying cause of machine failures. Getting to the real problem and underlying cause of machine failures.
Root cause analysis (RCA) is the process of discovering the root causes of problems in order to identify appropriate solutions. RCA assumes that it is much more effective to systematically prevent and solve for underlying issues rather than just treating ad hoc symptoms and putting out fires.
This root cause analysis (RCA) tree diagram example “Personal problem solution” was created using the ConceptDraw PRO diagramming and vector drawing software extended with the Seven Management and Planning Tools solution from the Management area of ConceptDraw Solution Park.
Tools for Root Cause Analysis Methods to Prevent Breaches in Infection Control for the Dental Practice
The root cause analysis (RCA) tree diagram example “Manufacturing problem solution” was created using the ConceptDraw PRO diagramming and vector drawing software extended with the solution “Seven Management and Planning Tools” from the Management area of ConceptDraw Solution Park.
Consider the following example: A worker slips . on a puddle of oil on the plant floor and falls. A traditional investigation may find the cause to be “oil spilled on the floor” with the remedy limited to cleaning up the spill and instructing the worker to be more careful. 5. A root cause analysis would reveal that the oil on the floor was merely a symptom of a more basic, or fundamental
• Root cause analysis helps identify what, how and why something happened, thus preventing recurrence. • Root causes are underlying, are reasonably identifiable, can be controlled by management and allow for generation of recommendations. • The process involves data collection, cause charting, root cause identification and recom-mendation generation and implementation. manipulating
For example, a manufacturing company’s overall goals (ideal state) are typically no safety injuries, no environmental issues, no customer issues, no production problems and …
Root cause analysis using Ishikawa diagrams may fail to distinguish between “necessary” and “sufficient” conditions. From the original example: the missing lock nut was “sufficient” to cause defects in one machine’s output, and so it caused the assembly problems. However, if excessive vibration can also cause slippage even if the lock nut were present, then it was not “necessary” for the lock
5 WHY analysis in itself is already a very strong tool for root cause analysis, but combining it with a fishbone analysis you really have the most powerful, yet easy to use and implement combination of tools for root cause analysis.
The 5 Whys problem solving technique uses a very simple iterative approach in analysing and attempting to find the root cause of a problem. The 5 why technique originates from the Toyota Manufacturing system pioneered in Japan by the Toyota car company. The concepts consist of defining the problem in a problem statement first and then asking why is this is the case, or why is …
Example of Automated Root Cause Analysis in Manufacturing A prime example of automated root cause analysis would be to look at how machine learning can be utilized to deduce the root cause of asset failure and quality deviations in manufacturing.
• The Root Cause associated with the escape of the defect to Ontic. The first page of this tutorial displays a flowchart depicting the suggested general thought process that may be used during the “Defect/Escape” Root Cause Analysis.
Root Cause Analysis 2016 MDH
When there is a production problem, root cause analysis can find a solution. Assuming that the question, “Why?” is asked often enough. When faced with a manufacturing problem, quality professionals at world-class organizations typically implement two types of remedial actions, known as “control of nonconforming product” and “root cause analysis
5-Why Analysis method is used to move past symptoms and understand the true root cause of a problem. It can be used with trend charts or pareto charts as a hybrid tool to guide problem-solving.
Root Cause Analysis of the Major Equipment Breakdown Problems of the Tube Section of a FMCG Company as an Approach to Improve OEE Papari Das1, – product design for manufacturing and assembly pdf Productivity Improvement by Root Cause Analysis in Manufacturing Industry analysis and the result of the example studies are encouraging. However, the studies are far from being practical one as they include too many parameters and assumptions. Vikash Dwivedi focuses on the quality improvement of one of the major defect in plastic injection moulding of components. One of the main defect
Productivity Improvement by Root Cause Analysis in
The 5 Whys Process We Use to Understand the Root of Open
5 Whys Problem solving and problem analysis to find root
Lean Problem Solving Zele 1107 Lean manufacturing
Root cause analysis examples in manufacturing ppt
Tools for Root Cause Analysis c.ymcdn.com
The most Powerful way to perform Root Cause Analysis
RMA Process and Root Cause Analysis in Manufacturing
– Example RCA Reports Apollo Root Cause
Root Cause Analysis Your Complete Guide
Root Cause Analysis in a World-Class Manufacturing Operation
How to apply the Fishbone diagram in a cutting tool
6 replies on “Root cause analysis examples in manufacturing pdf”
Leave a Comment• The Root Cause associated with the escape of the defect to Ontic. The first page of this tutorial displays a flowchart depicting the suggested general thought process that may be used during the “Defect/Escape” Root Cause Analysis.
Root Cause Analysis for Drugmakers FDAnews
Solving Manufacturing Problems 1. 8D Problem Solving Methodology 2. Containment 3. Defect Characterization 4. Failure Analysis 5. Defect Characterization Case Study 6. Root Cause Analysis Methodology 7. Prioritizing Corrective Actions 8. Validate that Corrective Actions Prevent Problem Recurrence 9. Leverage Countermeasures to Similar Products and/or Processes 10. Root Cause Analysis …
PROBLEM ANALYSIS. Root Cause Analysis Tree Diagram
(PDF) ROOT CAUSE ANALYSIS OF DEFECTIVES OF A MANUFACTURING
PO Box 301252 Phone 281.489.2904 ThinkReliability
• Root cause analysis helps identify what, how and why something happened, thus preventing recurrence. • Root causes are underlying, are reasonably identifiable, can be controlled by management and allow for generation of recommendations. • The process involves data collection, cause charting, root cause identification and recom-mendation generation and implementation. manipulating
PROBLEM ANALYSIS. Root Cause Analysis Tree Diagram
4 Root Cause Analysis for Drugmakers Introduction Wheneverregulatoryauthoritiesanywhereintheworldperformanauditofadrugmanufactur-er
RMA Process and Root Cause Analysis in Manufacturing
Root cause analysis examples in manufacturing ppt
Tools for Root Cause Analysis c.ymcdn.com
When there is a production problem, root cause analysis can find a solution. Assuming that the question, “Why?” is asked often enough. When faced with a manufacturing problem, quality professionals at world-class organizations typically implement two types of remedial actions, known as “control of nonconforming product” and “root cause analysis
(PDF) ROOT CAUSE ANALYSIS OF DEFECTIVES OF A MANUFACTURING
And the most common method of analysis for these problems is the root cause analysis tools (root cause analysis training). You can also see Gap Analysis Templates . Analysing into a defect by inspecting into every single aspect of the problem in a step by step analysis is the root cause analysis example.
Root Cause Analysis for Drugmakers FDAnews
Comments are closed.